Expert Guidance on What is Porosity in Welding and Exactly How to Resolve It
Expert Guidance on What is Porosity in Welding and Exactly How to Resolve It
Blog Article
The Scientific Research Behind Porosity: A Comprehensive Overview for Welders and Fabricators
Comprehending the elaborate devices behind porosity in welding is important for welders and fabricators making every effort for impressive workmanship. From the composition of the base products to the ins and outs of the welding process itself, a plethora of variables conspire to either aggravate or minimize the presence of porosity.
Comprehending Porosity in Welding
FIRST SENTENCE:
Exam of porosity in welding exposes crucial insights right into the integrity and high quality of the weld joint. Porosity, identified by the presence of tooth cavities or gaps within the weld metal, is a typical concern in welding processes. These spaces, otherwise correctly resolved, can compromise the structural stability and mechanical homes of the weld, bring about potential failures in the completed product.
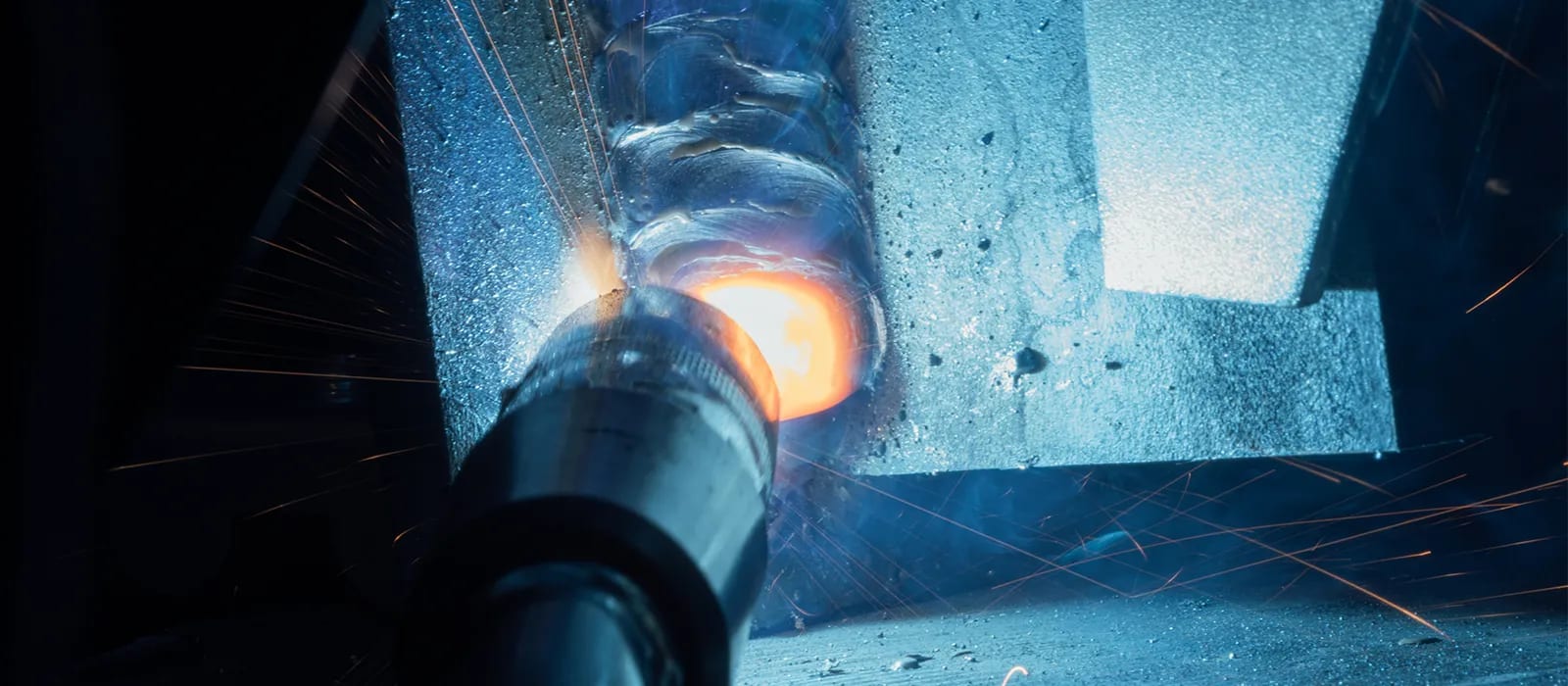
To discover and quantify porosity, non-destructive testing approaches such as ultrasonic screening or X-ray examination are commonly utilized. These methods enable the identification of inner flaws without jeopardizing the integrity of the weld. By analyzing the size, form, and distribution of porosity within a weld, welders can make informed choices to enhance their welding processes and attain sounder weld joints.
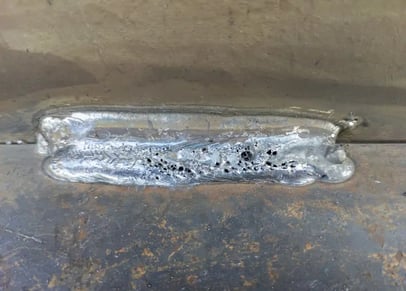
Aspects Influencing Porosity Development
The occurrence of porosity in welding is influenced by a myriad of aspects, ranging from gas shielding effectiveness to the complexities of welding specification settings. Welding specifications, including voltage, current, travel speed, and electrode kind, additionally influence porosity development. The welding method utilized, such as gas metal arc welding (GMAW) or shielded metal arc welding (SMAW), can affect porosity development due to variants in heat distribution and gas coverage - What is Porosity.
Results of Porosity on Weld Top Quality
Porosity formation substantially jeopardizes the structural integrity and mechanical residential properties of welded joints. When porosity is present in a weld, it develops gaps or cavities within the product, minimizing the general strength of the joint. These gaps function as tension concentration factors, making the weld much more susceptible to fracturing and failure under load. The visibility of porosity also damages the weld's resistance to rust, as the trapped air or gases within the gaps can react with the surrounding environment, causing degradation with time. Furthermore, porosity can hinder the weld's capability to withstand stress or impact, more endangering the total high quality and integrity of the welded framework. In vital applications such as aerospace, automotive, or structural building and constructions, where security and durability are vital, the detrimental impacts of porosity on weld top quality can have severe repercussions, stressing the significance of lessening porosity through appropriate welding methods and treatments.
Methods to Decrease Porosity
Furthermore, using the appropriate welding criteria, such as the proper voltage, present, and take a trip speed, is critical in preventing porosity. Preserving a consistent arc length and angle throughout welding helpful site also assists reduce the probability of porosity.

Making use of the ideal welding strategy, such as back-stepping or using a weaving activity, can additionally aid disperse warm uniformly and decrease the chances of porosity formation. By applying these strategies, welders can successfully lessen pop over to these guys porosity and create premium welded joints.

Advanced Solutions for Porosity Control
Implementing sophisticated modern technologies and ingenious methods plays a crucial function in achieving premium control over porosity in welding processes. One advanced option is using innovative gas blends. Shielding gases like helium or a combination of argon and hydrogen can help in reducing porosity by giving better arc security and improved gas insurance coverage. Furthermore, using advanced welding strategies such as pulsed MIG welding or modified ambience welding can likewise assist reduce porosity issues.
One more advanced remedy entails using innovative welding devices. Making use of tools with integrated attributes like waveform control and advanced power sources can enhance click here to read weld quality and decrease porosity risks. Moreover, the application of automated welding systems with exact control over criteria can significantly minimize porosity defects.
Furthermore, incorporating innovative surveillance and examination modern technologies such as real-time X-ray imaging or automated ultrasonic screening can help in discovering porosity early in the welding process, permitting immediate rehabilitative activities. Generally, integrating these advanced remedies can considerably enhance porosity control and enhance the total high quality of welded parts.
Final Thought
In final thought, understanding the scientific research behind porosity in welding is necessary for welders and producers to produce high-quality welds. By recognizing the elements affecting porosity formation and implementing strategies to reduce it, welders can improve the total weld high quality. Advanced solutions for porosity control can better enhance the welding procedure and guarantee a solid and dependable weld. It is necessary for welders to constantly educate themselves on porosity and carry out ideal methods to attain optimal outcomes.
Report this page